What Sets Native Trails’ Copper Sinks Apart?
An Heirloom-Quality Copper Sink Is All in the Details and the Hands That Touch It Along the Way
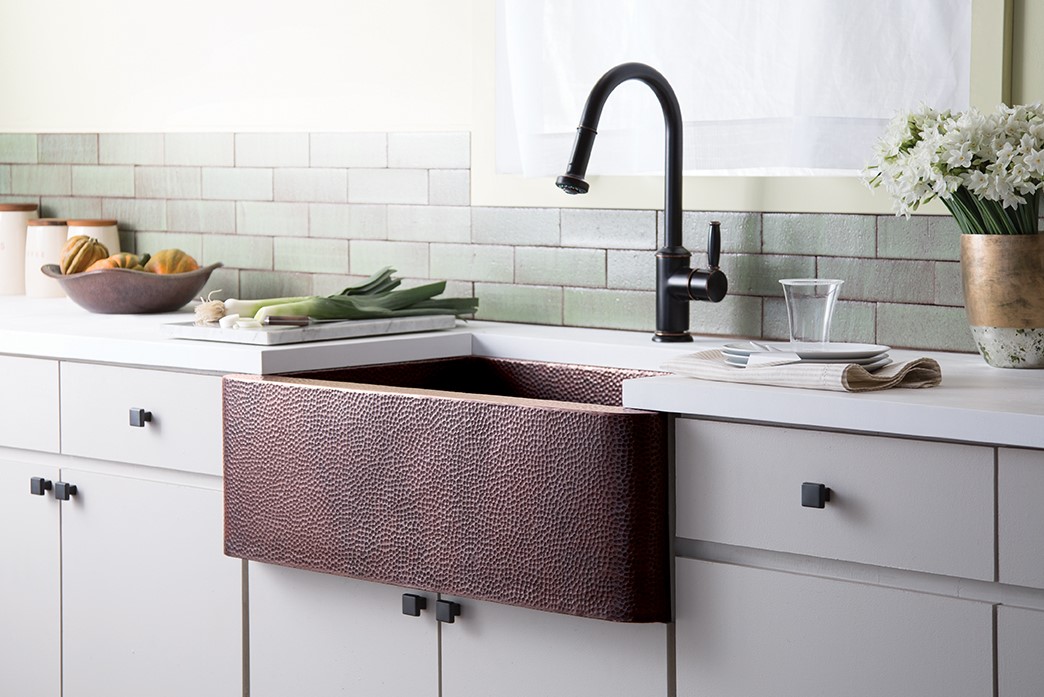
Most major hardware stores now sell copper sinks. As well as a growing variety of online retailers who want to cater to rustic tastes of modern homeowners. In this sea of copper sinks, it is difficult to determine which are the highest quality, what makes a copper sink high quality, and why it matters.
At Native Trails we have the art of making a luxury copper sink down to a science. We’ve been recycling copper into sinks since 1997. That’s when our founder Naomi Neilson decided to turn the relationships she’d formed with artisans in Mexico into a business. Copper bowls soon gave way to copper sinks. Today we work with many of the same artisans we did in the early days to develop the highest quality sinks in the industry. These are people for whom craftsmanship is a core value, a kind of inheritance. Many of them have passed down traditions of handicrafts, folk art and coppersmithing for decades.
Besides our award-winning designs, Native Trails is set apart by our commitment to sustainable manufacturing processes. We use only recycled copper and mix naturally renewable jute fiber into our cement to produce our lighter-weight and earth-friendly NativeStone® sinks. But our biggest differentiator occurs during the making of our copper sinks.
The Making of a Luxury Copper Sink
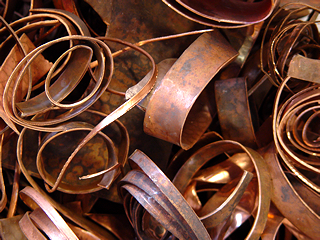
All of our copper sinks originate at foundries in Mexico with a pile of used copper wire and pipe. But there’s a marked difference between low-grade and high-grade copper. So, we don’t make use of every piece of copper that comes our way. It is the job of one of our artisans to sort through this pile of copper.
“We have a pretty extreme quality control process when sifting through the copper itself,” says Twin Ramirez, Native Trails’ longtime procurement manager. “The person who does this now has years of experience dictating what’s copper and what’s not. He pulls out the pieces that aren’t copper and separates them one by one.”
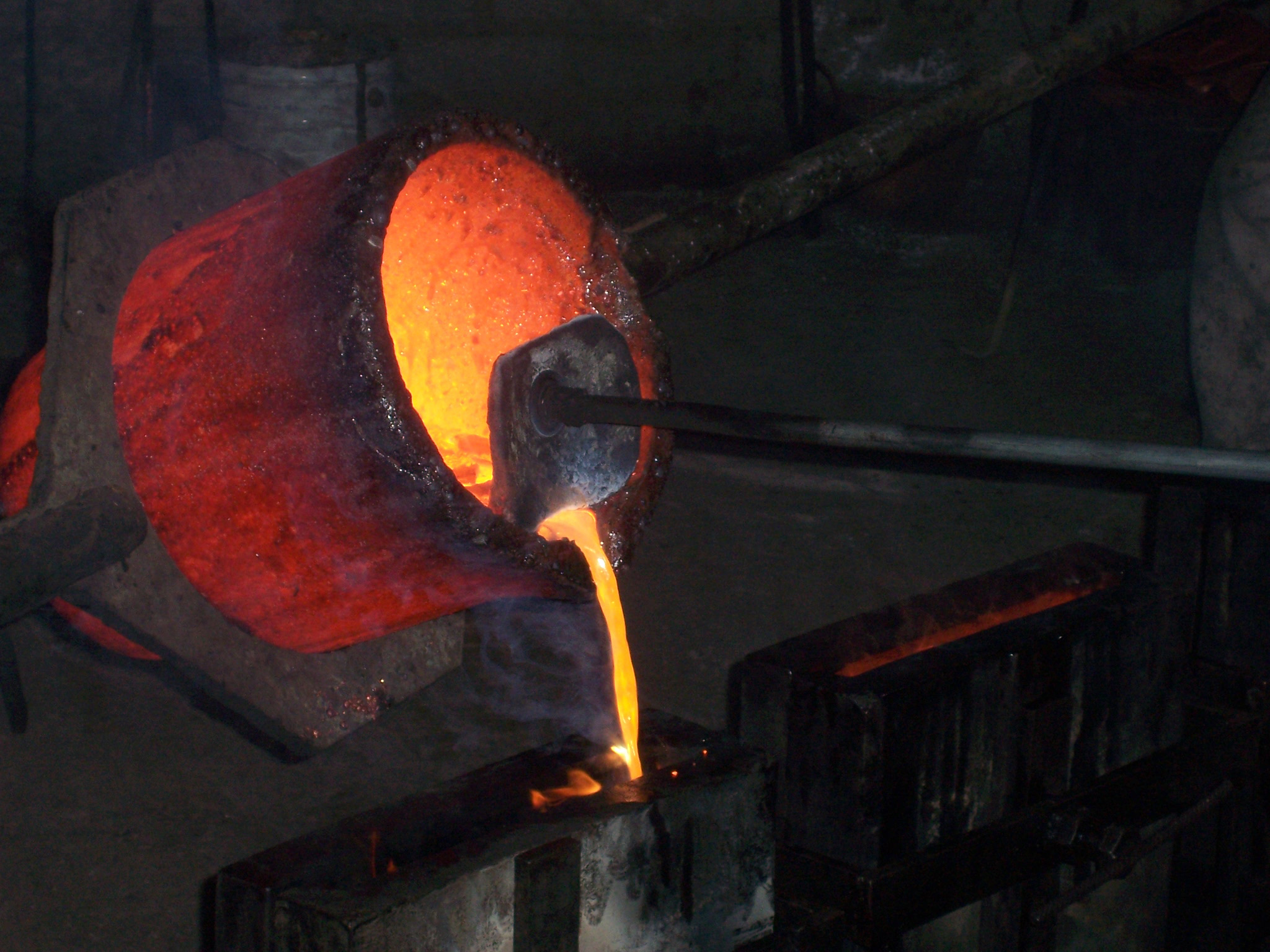
The copper that makes the cut is placed into a melting pot and melted at a temperature above one thousand degrees Celsius. This intense heat helps remove small defects that aren’t visible to the naked eye as well as anything in the pot that’s not pure copper. The artisans the remove any imperfections that rise to the top.
They pour the heated copper into a square, steel mold which turns into large sheets roughly two inches thick. As it cools it hardens, and there is some more processing that happens at this point. Meanwhile, our artisans clean up the copper and get rid of all the sharp edges.
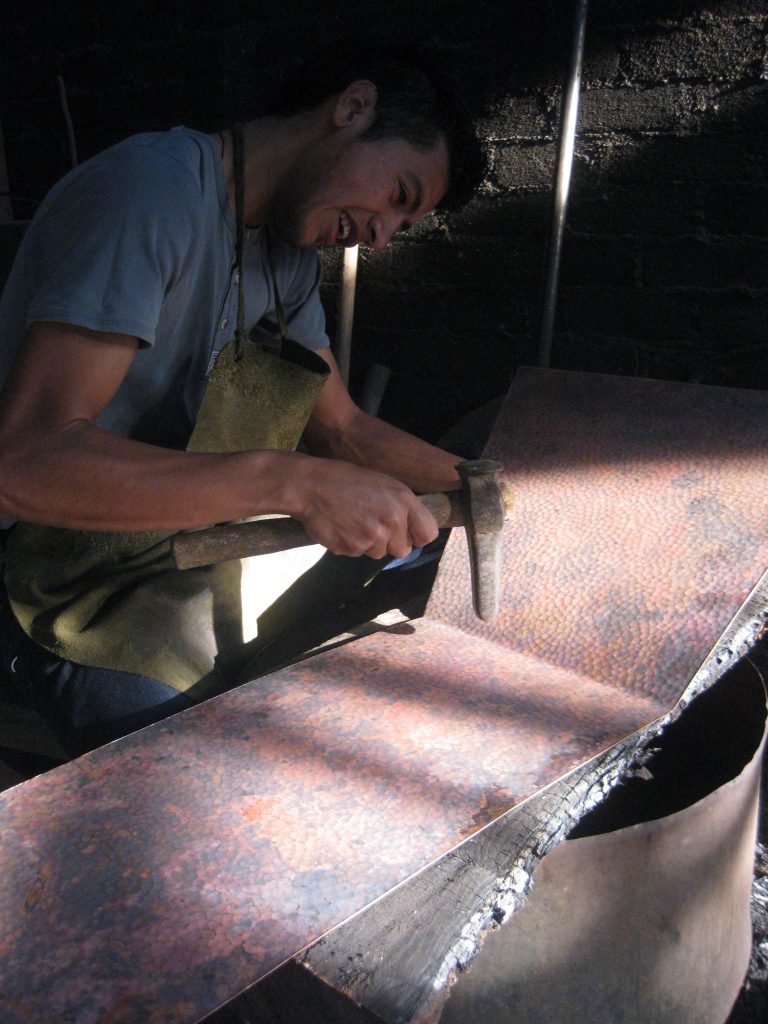
These sheets of copper are next run through a machine that thins it out until it reaches the proper gauge. All of our kitchen sinks are 16-gauge, and some of our smaller lavatory basins are 18-guage. “I have no idea what that machine is called in English,” says Twin, who converses with all of our artisans in Spanish.
“When we have new designs, we have the opportunity to work more closely with our artisans,” says Twin. “They give us feedback in terms of the design itself, and then they’ll make prototypes and send them up here [to Native Trails’ headquarters in San Luis Obispo]. We’ll potentially adjust them, focusing on the slopes and curves of a product. We’ll sometimes review multiple prototypes of the same piece to get it exactly how we like it.”
Once the ideal thickness has been achieved and the copper has gone through some additional cleaning and brushing to take out any last imperfections, the copper sheets are heated until they’re soft enough to work with. Each artisan picks which side of the copper will be the face and which will be the back.
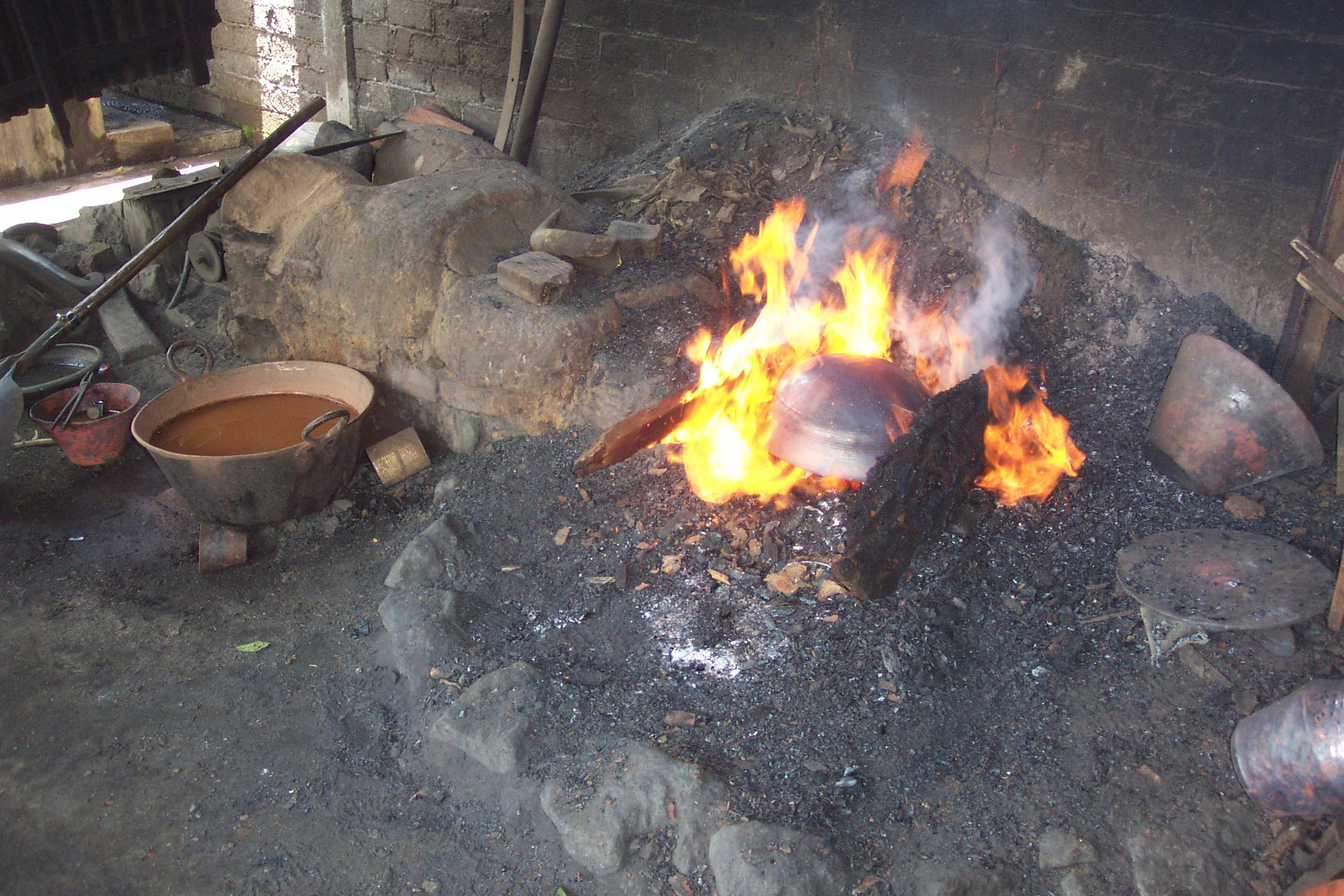
This is when the hammering process starts. “You typically have one guy who hammers the same sheet of copper, and he’ll strike away until the entire sheet is completely formed. We have multiple artisans who do this, but there’s only one artisan per sheet to avoid different hammer strokes. I might hammer differently than you, so we all get our own sheet. Likewise, if we’re making a big bathtub, the sheets used to make that bathtub are all hammered by the same person because the sheet that I hammered might look a little bit different than the sheet you hammered.”
After the entire sheet has been hammered, the artisans at last turn the copper into sinks. If it’s a kitchen sink, they do this by molding and welding the copper. Our smaller bowls go through a slightly different process. First, artisans form them into an oval or round shape and then hammer. This is the same process for all of our Native Trails Lifestyle products. They then send our copper products that go on to become Brushed Nickel to the US to be plated and hand-brushed.
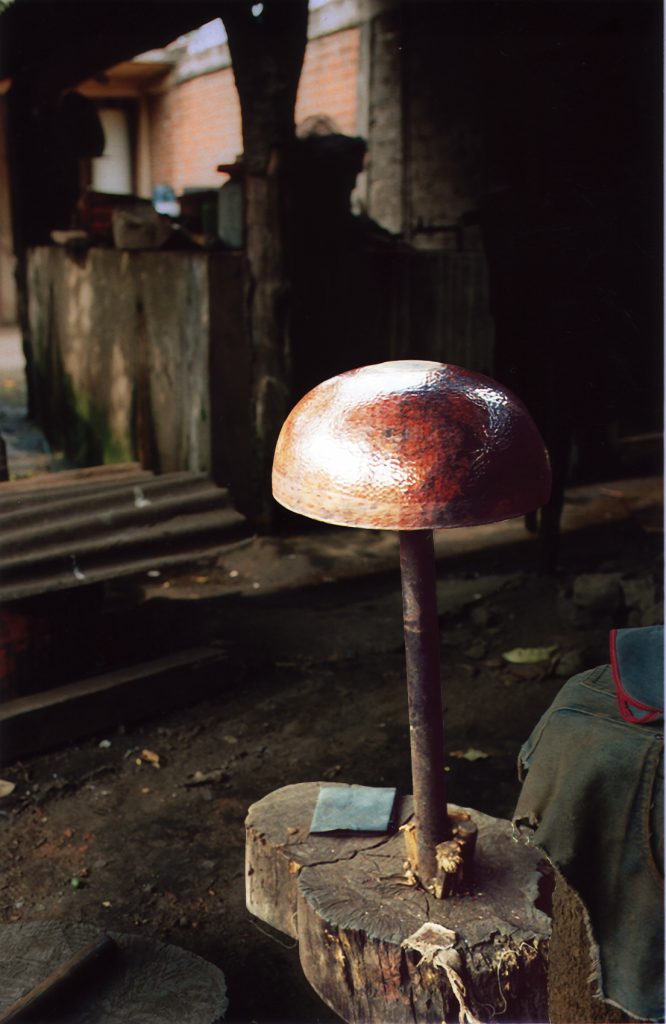
Before being sent to California, the artisans inspect the copper sinks a couple more times. When they arrive in San Luis Obispo we reinspect them one by one and give them a final cleaning before they’re shipped to you.
Having gone through this incredibly rigorous process, our sinks and bathtub are made to be heirloom-quality and are backed with a lifetime guarantee. Which is why they’ve landed in some of the finest homes in the world.
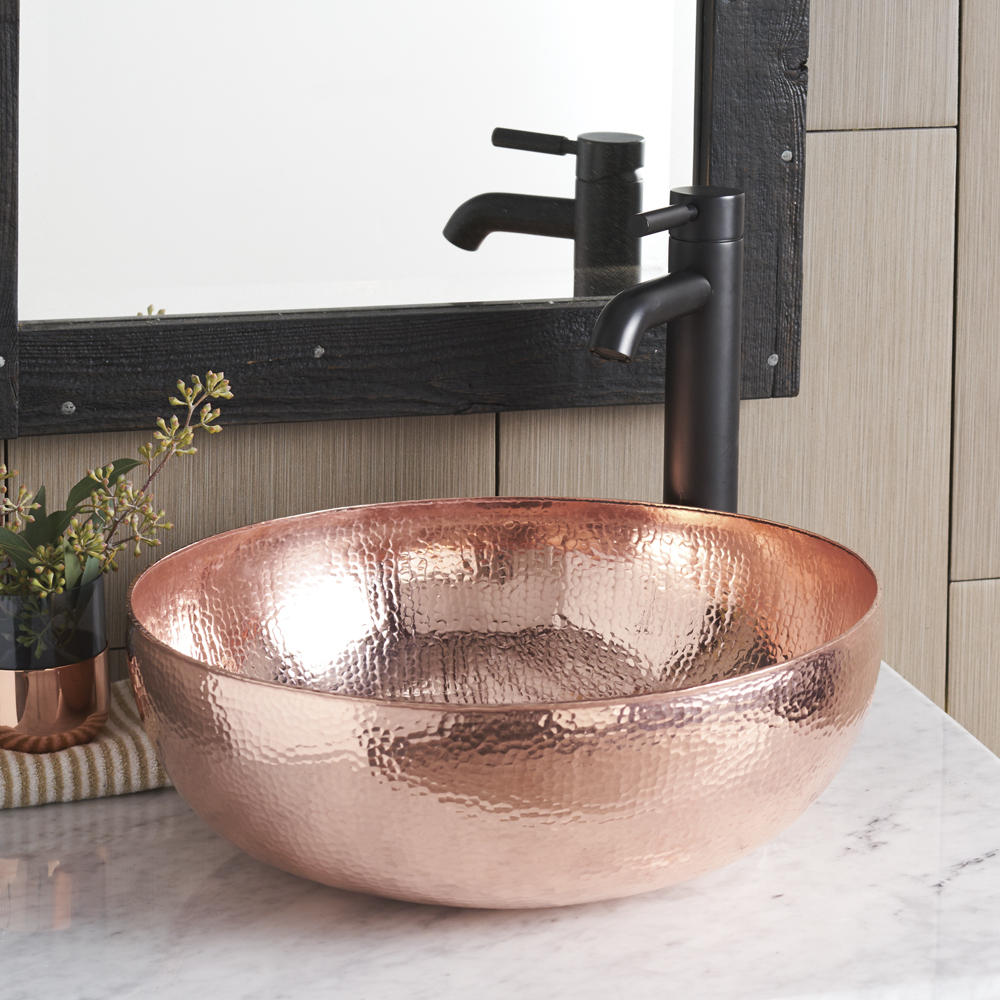
At Native Trails it’s our quality control and the care afforded by so many skilled hands that turn an ordinary copper sink into a luxury copper sink.